How Toyota Motor Europe is Optimising Post-Production
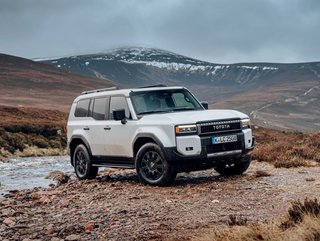
Part of one of the largest automotive corporations in the world, Toyota Motor Europe oversees the wholesale sales and marketing of Toyota, GAZOO Racing and Lexus vehicles and parts and accessories, as well as Toyota’s European manufacturing and engineering operations.
Toyota has invested almost US$12bn in Europe since 1990. Its eight manufacturing plants in the region are located in Portugal, the UK, France, Poland, Czech Republic and Turkey.
At the heart of Toyota Motor Europe’s supply chain are seven strategically-located vehicle distribution hubs that handle both the European-built models and those shipped to Europe from overseas.
These hubs ensure all vehicles get to their customers on time, performing final installations on the vehicles and a final inspection before shipping the vehicles to their retailer.
Toyota Motor Europe looks to Artelys
Achieving delivery on time, while reducing lead times and CO2 emissions, is critical to Toyota Motor Europe’s distribution hubs.
That’s why the business has been working alongside Artelys, a specialist in numerical optimisation, modelling and decision support, which used FICO technology to build a solution that optimises post-production activity – organising tens of thousands of operations on thousands of vehicles every day.
Manual scheduling that once took three hours per day for each hub is now being completed in 20 minutes.
Customers buying vehicles from Toyota retailers can add numerous options such as a navigation system, tow bar or park assist. Artelys’ solution has increased the efficiency of the distribution hubs run by Toyota Motor Europe, ensuring satisfactory delivery time to customers and reducing the carbon footprint of vehicle logistics operations.
The solution optimises the work plan at each hub, maximising the number of tasks that can be performed considering various technical and operational constraints. These constraints vary widely, from restricting vehicle movements within the facility to ensuring compliance with legal working hours for the team.
“The flexibility of FICO Xpress and Artelys Kalis was key to addressing the very specific scheduling needs of Toyota’s workshops,” explains Nicolas Omont, VP Operations at Artelys.
“It’s particularly hard to design applications able to efficiently manage heterogeneous constraints and objectives and prioritise them. In addition, the software is able to manage optional flexibility by enabling potential overtime to finish high-priority tasks or diversify crews working on difficult tasks.”
FICO optimisation solves supply chain problems
User acceptance was also essential to the implementation of Artelys’ solution for Toyota Motor Europe.
Artelys showed planners they wouldn’t lose flexibility in their way of working or have a black box providing plans without being able to understand them. Planners are able to analyse the application output and understand differences from their current way of working.
The solution must solve planning every day in a few minutes to allow sufficient time for planners to validate it. In addition, it can re-optimise based on end-user manual amendments.
“This kind of optimisation will only gain in importance as manufacturers worldwide look to reduce their carbon footprint while maximising performance,” adds Alexandre Graff, VP of Global Partners & Alliances at FICO.
“Artelys has demonstrated with this project and others the massive potential of using FICO optimisation to solve incredibly challenging supply chain problems.”
******
Check out the latest edition of Supply Chain Magazine and sign up to our global conference series – Procurement and SupplyChain LIVE 2024.
******
Supply Chain Digital is a BizClik brand.
- Procurement & Supply Chain LIVE New York 2024: Day Two RecapDigital Supply Chain
- Submissions Closed: Global Procurement & Supply Chain AwardsDigital Supply Chain
- Sustainability Shines Through on P&SC LIVE New York Day OneSustainability
- Celebrating International Supply Chain Professionals DayOperations