Industry 4.0 Tech Paves Way for Predictive Maintenance
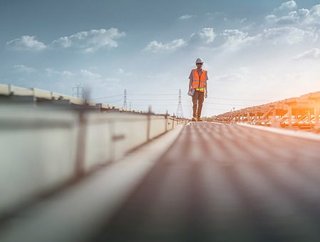
Today’s availability and low cost of digital technologies is fuelling the change of linear supply chains into always-on dynamic integrated networks, which are characterised by a continuous flow of information and analytics, and the merging of the physical and the digital.
The key phrase here is ‘always on’, because for any company – especially manufacturers – there is no time so costly as machine downtime.
Unplanned downtime can cost industrial manufacturers billions of dollars annually. Nearly half of such incidents are caused by equipment failure. Traditionally, such failure has been addressed retrospectively, through reactive maintenance programmes.
However, predictive maintenance can help control these costs by enhancing performance awareness and reducing downtime.
Predictive maintenance is the practice of analysing collective data from sensorized equipment using advanced analytics, the aim being to predict when a part is likely to fail, and thus when maintenance should take place.
The real-time flow of information, and the ability to analyse it, uses physical data to develop digital insights and drive informed physical action in the form of maintenance and upkeep.
Algorithms are used to analyse historical data, coupled with data relating to new environments, as well as user and machine data.
To better predict performance thresholds, alerts can signal when an asset is performing outside of an established threshold, so a technician can be scheduled, and spare parts ordered in advance of the asset breakdown.
In many respects, predictive maintenance is the point at which IT and operations technology (OT) meet. Whereas IT is the tech backbone of an organisation – monitoring, managing, and securing core functions such as email, finance and human resources – OT connects, monitors, manages and secures an organisation's industrial operations. Businesses engaged in activities such as manufacturing, mining, oil and gas, utilities, and transportation, among many others, rely heavily on OT, and such organisations are increasingly turning to the so-called ‘connected workforce’ model.
Paul Downey is Head of Manufacturing Marketing with Nokia’s Enterprise Campus Edge team, where he focuses on the drivers, use cases and implementation of digitalisation for the discrete and process manufacturing sectors.
“A connected workforce is one that is digitally integrated within organisations’ OT and IT manufacturing ecosystems,” Downey Explains. “It is where workers can seamlessly interact with colleagues, and can access relevant operational data from connected assets, such as autonomous robots and production-line equipment, and can effectively collaborate within manufacturing systems.”
Downey says access to the right data and information, at the right time “enables people, machines and processes to work as one”, adding that this “provides workers with new capabilities at the point where they need to make effective decisions and take appropriate actions”
He explains that connecting people and assets helps organisations continuously monitor asset-health data and that potential issues can prompt alerts that are sent to maintenance team members’ devices.
Downey says: “Protecting existing investment is often a priority and many manufacturers struggle with connecting legacy vehicles, machines and other equipment to a private wireless network to access OT data.
“This can be easily managed using ruggedised routers and dongles, allowing manufacturers to implement autonomous operations, predictive maintenance and other innovative use cases.
“Workers can access OT data over devices such as ruggedised smartphones and tablets.”
Attesting to the importance of predictive maintenance is Ruchir Budhwar, EVP Manufacturing Europe at Infosys.
Budhwar is acutely aware that resilient manufacturing operations form the bedrock of resilient supply chains.
He says: “A major lesson for manufacturers from the events of the past few years is that agility and resilience are key to survival.
The good news is that there are several digital technologies that manufacturers can leverage to make their operations more responsive, resilient and robust. Manufacturing cloud, connected technologies – digital twins, 5G, AR/VR – and AI should rank at the top of their consideration set.”
He says such tech supports tasks including inspecting product quality, monitoring remote sites and conducting predictive maintenance.
He adds: “Digital technologies, along with industrial data lakes, connect various systems in real-time to create seamless information flows and visibility across the supply chain.
“This enables complete automation of the supply chain to make it more flexible, agile and resilient.”
**************
Supply Chain Digital is a BizClik brand