IoT tech streamlining supply chain in its hour of need
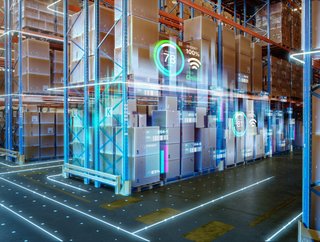
Global supply chains have been severely impacted by the Russo-Ukrainian conflict and the COVID-19 pandemic, with disruptions caused by such events leading to manufacturing delays, shipping complications, panic buying, and increased energy costs.
But with the rise of IoT devices revolutionising the way organisations around the world operate, offering a wealth of benefits across global supply chains, new technologies are helping businesses streamline their supply chains, increase efficiency, reduce costs, and improve visibility across the entire process.
The fourth industrial revolution, Industry 4.0, relies upon IoT to join operational and informational technology, for the sake of improving quality, reducing risk and minimising cost. “IoT is a core part of Industry 4.0 because it allows us to build digital networks of machinery, devices, and infrastructure. By using IoT, organisations can assemble smart factories and supply chain processes which continuously collect data,” says David Beamonte Arbués, Product Manager (IoT & Embedded Products) at Canonical.
“Businesses can then apply AI and ML technologies which, once synchronised, remove silos in the supply chain process and allow unprecedented levels of transparency, automation, insight and control,” Arbués adds. “Industry 4.0 focuses heavily on interconnectivity, automation, ML and real-time data. It marries physical production and operations with smart technology – none of which would be possible without IoT at its core.”
Improved visibility in supply chains
One of the most significant benefits that IoT technologies offer for supply chains is improved visibility. IoT devices can be integrated into every stage of the supply chain, from production to delivery, allowing businesses to track their goods in real time. This increased visibility enables businesses to make informed decisions about inventory management, transportation, and production schedules, which can lead to significant cost savings and improved customer satisfaction.
In many cases, such information is also combined with third-party data sources, allowing organisations to react quickly to unexpected supply chain events, such as extreme weather events, geopolitical instability or sudden dips in customer demand.
“Some of the recent supply chain disruptions we have seen are due to a lack of real-time visibility across the supply chain. For a well-functioning supply chain, across multiple levels, you must collect, integrate and analyse data to provide a single view of the supply chain”, explains Bjorn Andersson, Senior Director of Global IoT at Hitachi Vantara.
“This view should include data from sensors and devices, such as data associated with temperature and vibration. IoT enables this level of visibility, allowing you to see if suppliers can meet their commitments, or to spot when a proactive action needs to be taken to prevent a disruption in production.”
IoT devices can also help businesses optimise their supply chains by providing real-time data on the performance of equipment and machinery. This data can be used to identify potential issues before they become major problems, helping reduce downtime and improving overall equipment performance, leading to increased productivity and cost savings.
Predictive maintenance
Data-driven predictive maintenance solutions are helping businesses with profitability, sustainability and the personal safety of their people.
According to SAP, predictive maintenance seeks to prevent equipment failure and downtime by connecting IoT-enabled enterprise assets, applying advanced analytics to the real-time data they deliver, and using the resulting insights to inform educated, cost-effective, and efficient maintenance protocols.
Today’s predictive maintenance has its roots in supervisory control and data acquisition (SCADA) - a control-system architecture formed of computers, networked-data communications and graphical user interfaces for high-level supervision of machines and processes, for assets either in situ or in remote locations.
“SCADA has been around for 40 years,” says Andy Hancock, Global VP of SAP’s Digital Supply Chain Centre of Excellence (CoE). “But Industry 4.0 technologies such as AI, ML and IoT have taken it to a whole new level of sophistication.
“SCADAs were all about condition-based monitoring,” he adds. “So, ‘If this happens, then do that’. But what people increasingly want is a predictive element, such as gaining insight into the useful remaining life of an asset somewhere out in the field. With big data, it’s now possible to carry out trend analysis to get at this kind of information.”
- US$200bn: The enterprise IoT market grew 21.5% to $201 billion in 2022
But Hancock warns that data-driven solutions can also bring their own problems.
“With predictive maintenance, you should always be looking out for the exception,” he says. “Think of a temperature gauge on a piece of equipment, which is feeding back data. If everything is running fine, it will always be roughly the same temperature. You don’t need to keep feeding back data about that piece of equipment. The only data you want to capture is if something changes - say if the thermostat fails.
“With data, less is usually more. Systems can soon get inefficient if overloaded with data. And then you end up chucking more tech at the problem, where what you really need to do is cut back on the data.”
The next level
Predictive maintenance might feel like a new concept to many, but, says Hancock, some companies are already taking things to the next level, using tech to help drive something called “prescriptive maintenance”.
He says: “Imagine you have two identical assets. One's nicely tucked inside a factory and so is in a fairly constant environment, but the other asset is exposed to the elements on the seafront. Clearly, you’re going to have different performances from those two assets, and so you create prescriptive maintenance cycles that take environmental conditions into account.”
Having fine-tuned maintenance cycles - whether predictive or prescriptive - is important for preventing over-maintenance as much as under-maintenance, Hancock stresses.
With sustainability now an issue of utmost importance for businesses, the green gains of predictive maintenance solutions are also very appealing.
“If you're over-maintaining an asset, you’re wasting money and resources,” Hancock concludes. “Why do an overhaul every six months when it’s not necessary? With predictive maintenance, you can use historical information via IoT sensor data and extend the maintenance cycle to seven or eight months, with no negative impact on the machinery.”