How can additive manufacturing benefit the supply chain?
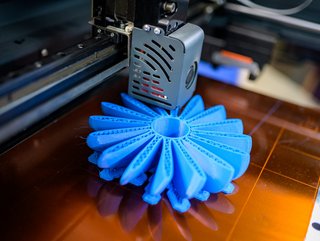
Stratasys recently hosted a roundtable discussion with three high-profile, international corporations who relayed their experiences of 3D printing over the past two challenging years. Taking part were Octavio Pichardo Romero, senior manager, General Motors production plant, San Luis Potosi, Mexico; and from Europe, Philip Emmerling, business development additive manufacturing, Siemens Mobility; and Barbara Bergmeier, head of operations, Airbus Defence and Space.
The benefits of 3D printing in manufacturing to the supply chain
The manufacturing benefits of 3D printing/additive manufacturing (AM) are now widely known. Less known is its growing importance in the global supply chain. Recent disruptions in normal supply chains have highlighted vulnerabilities and AM has made a crucial difference to manufacturers.
From being a technology for the development of prototypes, specialist parts, tools and jigs, AM, as the roundtable participants explain, has not only moved into mainstream manufacturing but also become a driver in strategic development.
For many years, the GM plants in Mexico have used 3D printing for making production parts for high performance vehicles, including metal parts for the Cadillac V series. However, in the past year, the company has used it to 3D print spare parts for equipment on its assembly line, ensuring that production could continue when parts needed to be replaced.
“When supply chains were interrupted during the pandemic, getting a number of small but critical parts became very difficult,” said Octavio Pichardo Romero. “One such part was in our paint shop where the Bakelite bushings in a large mechanism for moving truck chassis need periodic replacement. These bushings need to provide insulation of 200A, 300V, so they are specialist pieces. Normal deliveries are two-to-three months from ordering, and the components last about four months, so regular replacement is the norm.
“To avoid shutting down the line, we worked with the supplier, chose the right material, and 3D printed effective replacement parts,” he continued. “We are able to print the part in five hours, avoiding line closures that would cost around US$1,000 per hour. Another example was when the development of a new transmission required a special socket wrench for a redesigned cap. Because the design was new, there was not a commercial option that would deliver the proper torque. Traditionally manufacturing one could take months. Again, working with the OEM supplier, we were able to 3D print them using a high-tech industrial grade material and have one in our hands within just a few hours.
“Sometimes, a very small part can cause lengthy delays. At one point, we needed locating pins on an assembly line. Covid, delivery times from the US were four to six weeks, and from Japan, it would have taken ten to twelve weeks. Now, we 3D print them in twenty minutes. These examples and others have kept us running. The technology has made us rethink our supply chains, and how we can produce more parts locally,” Pichardo Romero concluded.
For Siemens Mobility, 3D printing was used in a different way to overcome pandemic-induced supply chain interruptions.
“At Siemens, we produce certified metal and polymer 3D printed parts for our customers worldwide, especially in the rail business,” Philip Emmerling explains. “3D printing technology is very important for us in the maintenance of trains where our goal is to carry out on-demand printing for tailored product solutions. We are now using AM to optimize the supply chain, especially in the area of maintenance where there is a need for fast, quick and reliable solutions for spare parts. In this sense, we are doing similar things to Octavio in Mexico.
“From our Digital Depot, in Dortmund, inspections are undertaken on trains while still in service and maintenance can be scheduled and parts ordered before the train comes into the depot,” he says. “The challenge is planning, ordering and purchasing spare parts, but this is where AM has a lot of benefits compared to conventional supply streams.
“For us, AM has been the perfect solution,” he states. “It is very fast and scalable. We have printers around the world. Not much space is needed; you don't need a big manufacturing hall or a lot of machinery – and this was the core of our idea to build a global 3D printing network.
“At the centre of this network is the Centre of Competence which handles R&D, engineering work and designs for parts. Each ‘satellite’ is connected to the Centre of Competence,” Emmerling says. “They contact us and we create the solution with them. It's a tailored solution that the satellite can put directly on the 3D printer. Our Stratasys 3D printers are really perfect for that; we can do the main work – the preparation, the engineering and preparation of the part, then they can produce it directly in their depot. This virtually eliminates conventional supply chains and saves shipping, warehousing, administration, customs and other time and cost factors – which also makes AM a very sustainable solution,” Emmerling concludes.
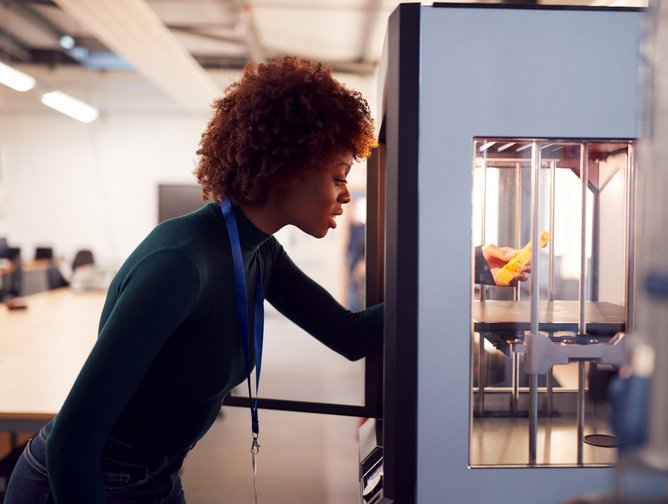
Ensuring sustainability rules in the manufacturing supply chain
While the challenges are similar for Airbus Defence and Space, the priorities are different.
“At our sites around Europe, Airbus uses AM for some well-defined purposes – one of which, like Siemens Mobility, is sustainability and the reduction of our environmental impact,” Barbara Bergmeier explains. “Octavio and Philip have already mentioned reduced lead times, and this has proved to be a big lever for people and employee engagement. A lot of ideas come from our people, especially on the shop floor, and AM printing enables more of these ideas to be tested and evaluated.
“We also use AM to boost product and people safety – which is our top priority – and one final, very important topic: freedom of design. Altering materials helps to reduce the weight of components and reduce the CO2 impact of an aircraft.
“As regarding supply chains, using AM makes us less dependent on suppliers, whether it’s raw material or finished parts, and that reduces our supply chain dependence, but what I really like is that we do not waste as much material. In some cases, 80% material savings are made. In aircraft manufacturing, there are important links between less materials, less weight, less energy required and less fuel consumed.
“So, we produce parts like Siemens Mobility, but we also 3D print jigs and tools as at GM. This gives us more independence and reduces the reliance on deliveries, Barbara Bergmeier concludes.
From spare parts, making jigs and tools, enabling affordable new part development, and networked distributed 3D printing, AM is changing manufacturing around the world.
Providing a holistic perspective on the experiences of these manufacturers and others like them, Andy Langfeld, President, EMEA, Stratasys, believes that the pandemic exposed the weaknesses in global supply, but developments in AM technology have clearly provided a solution.
“What we’re seeing today is more and more manufacturers leveraging this as an opportunity to rethink and reset their supply chains in order to become even more resilient and more agile to future disruption,” he says. “At the same time, technological developments within AM are enabling manufacturers to move from printing batches of tens to the production of thousands – even tens of thousands – of units, quicky and cost effectively. This is a game changer that is actively giving manufacturers further opportunity to increase the flexibility of 3D printing across more parts of the supply chain,” Langfeld concludes.
- Procurement & Supply Chain LIVE New York 2024: Day Two RecapDigital Supply Chain
- Submissions Closed: Global Procurement & Supply Chain AwardsDigital Supply Chain
- Sustainability Shines Through on P&SC LIVE New York Day OneSustainability
- Celebrating International Supply Chain Professionals DayOperations